Advanced Fracture Analysis
In the intricate world of engineering and technology, where precision and reliability are paramount, ensuring the structural integrity of components and assets is not just a necessity but a cornerstone of safety and integrity.
BEASY software allows engineers to determine the risk of failure due to defect in various types of components and structures.
Rather than using standard handbook solutions and calculations, engineers are able to model crack growth using real material properties and geometries, without the need to define complex crack orientations.
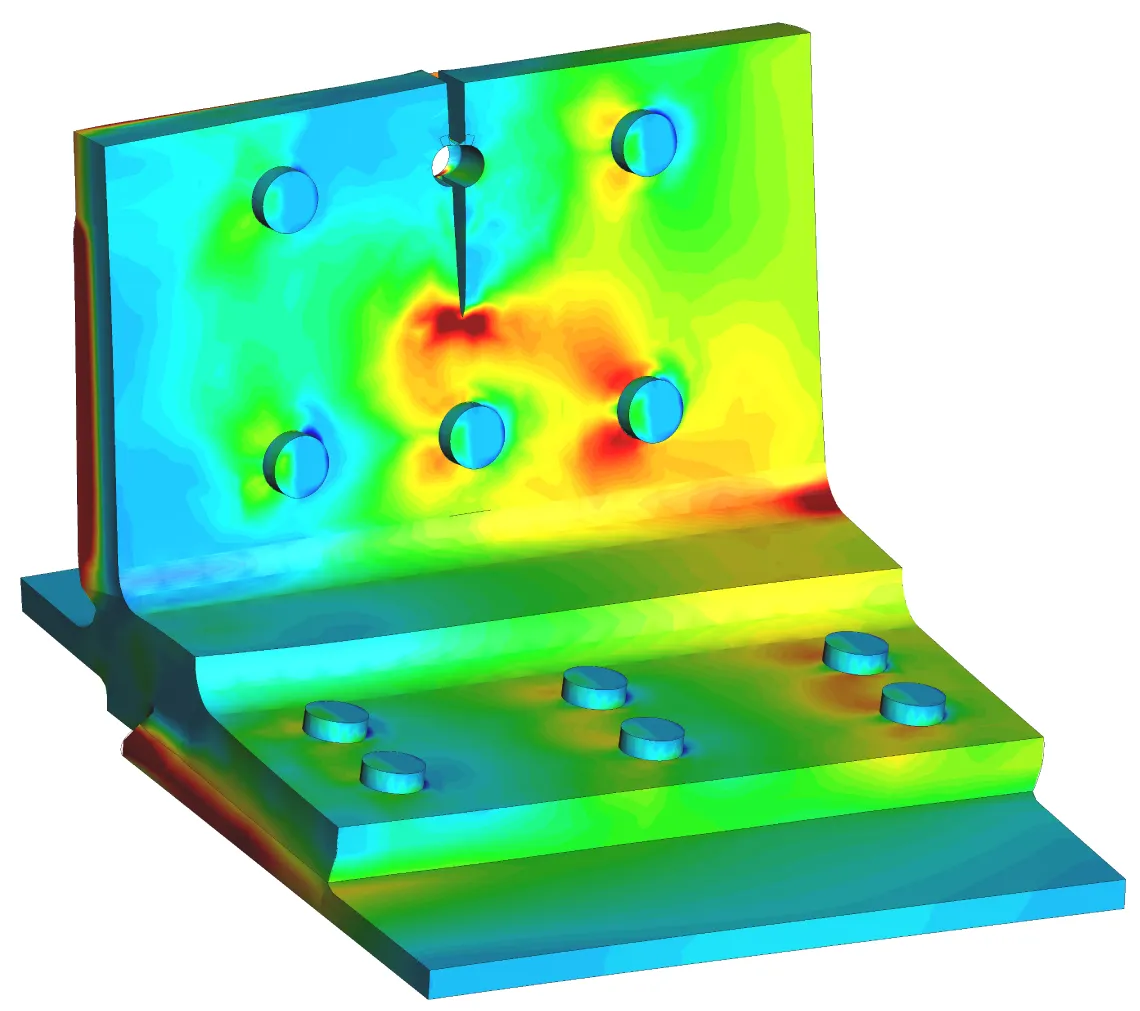

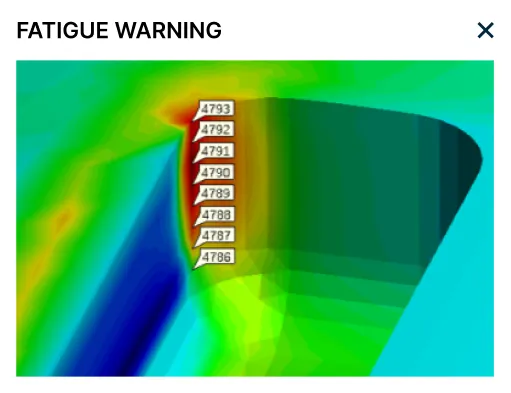
Common types of fracture:
Stress Corrosion Cracking (SCC)
Stress corrosion cracking occurs when a crack grows under a sustained, and normally steady, load. These types of cracks are typically slow to grow and can occur before fatigue growth takes over.
Fatigue Crack Growth
Fatigue crack growth occurs when a repetitive cycle of load from minimum to maximum levels are applied to a component.
Forced Crack Growth
Force crack growth is a crack that growth that is not directly related to the physical behaviour or the component, but rather due to external factors such as mechanical forces or environmental factors.
Our simulation software and engineering consultancy stands as a beacon of excellence in simulating fracture, fatigue, and crack growth.
Working with industries that shape the world, we enable our clients to forge ahead with confidence, knowing that their engineering projects are supported by decades of experience, and a passion for innovation.
In industries where the tiniest flaw can lead to catastrophic consequences, predicting and preventing fractures is a must.
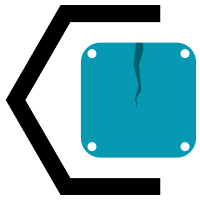
Fracture & Crack Growth
BEASY Fracture & Crack Growth (FCG) is a breakthrough solution for engineers seeking precise fracture mechanics models for structural components. This innovative technology allows for damage-tolerant design assessment with accurate stress intensity factor (SIF) solutions and three-dimensional crack growth simulations, gaining vital insights into crack growth rates and shape evolution.
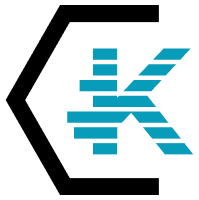
FASST
Revolutionise stress analysis models by scanning simulation models to pinpoint potential areas of crack growth. With BEASY Defect Scanner, engineers can scan stress models and easily gain insights into estimating critical crack sizes within areas of structures and components. These simulation models provide enhanced understanding of structural integrity and allow for predictive maintenance.
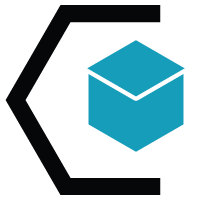
Other
Along with BEASY’s extensive range of stand-alone software, we offer a variety of add-ons to assist engineers and systems designers with their workflow and processing. This also allows models created in third-party software to benefit from BEASY’s powerful simulation and time-stepping capabilities.
Have a Consultant Contact You
Industry Leading Detection & Prevention For You
BEASY's software products and services help organisations solve complex engineering challenges.
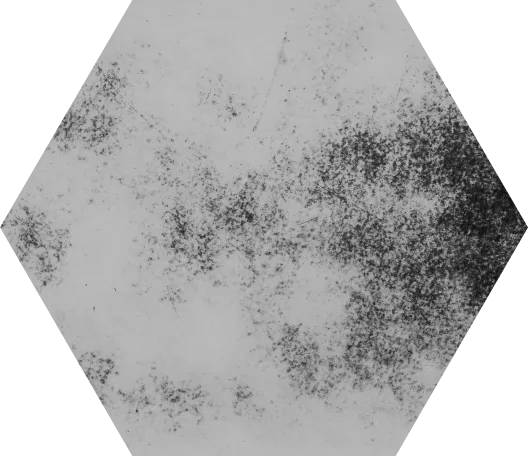
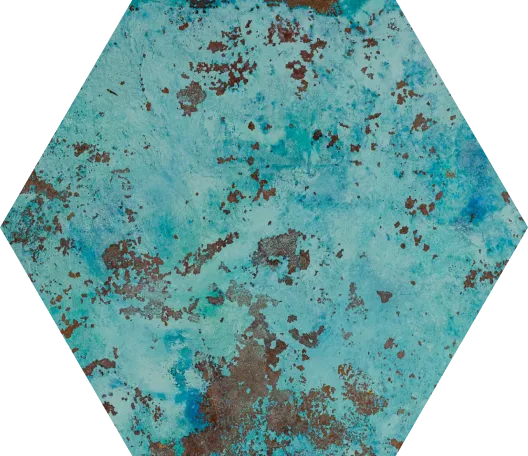