Corrosion
In the challenging world of engineering and technology, where precision and reliability are paramount, ensuring the structural integrity of components and assets is not just a necessity but a cornerstone of safety and integrity.
Recognising the impact of corrosion and the importance of cathodic protection (CP) systems, our engineers have developed advanced simulation technologies to accurately predict corrosion patterns and evaluate corrosion control systems. We are committed to pushing the boundaries of what is possible, drawing on years of experience to drive safety, efficiency, and innovation in industries including aerospace, defence, offshore, and oil & gas.
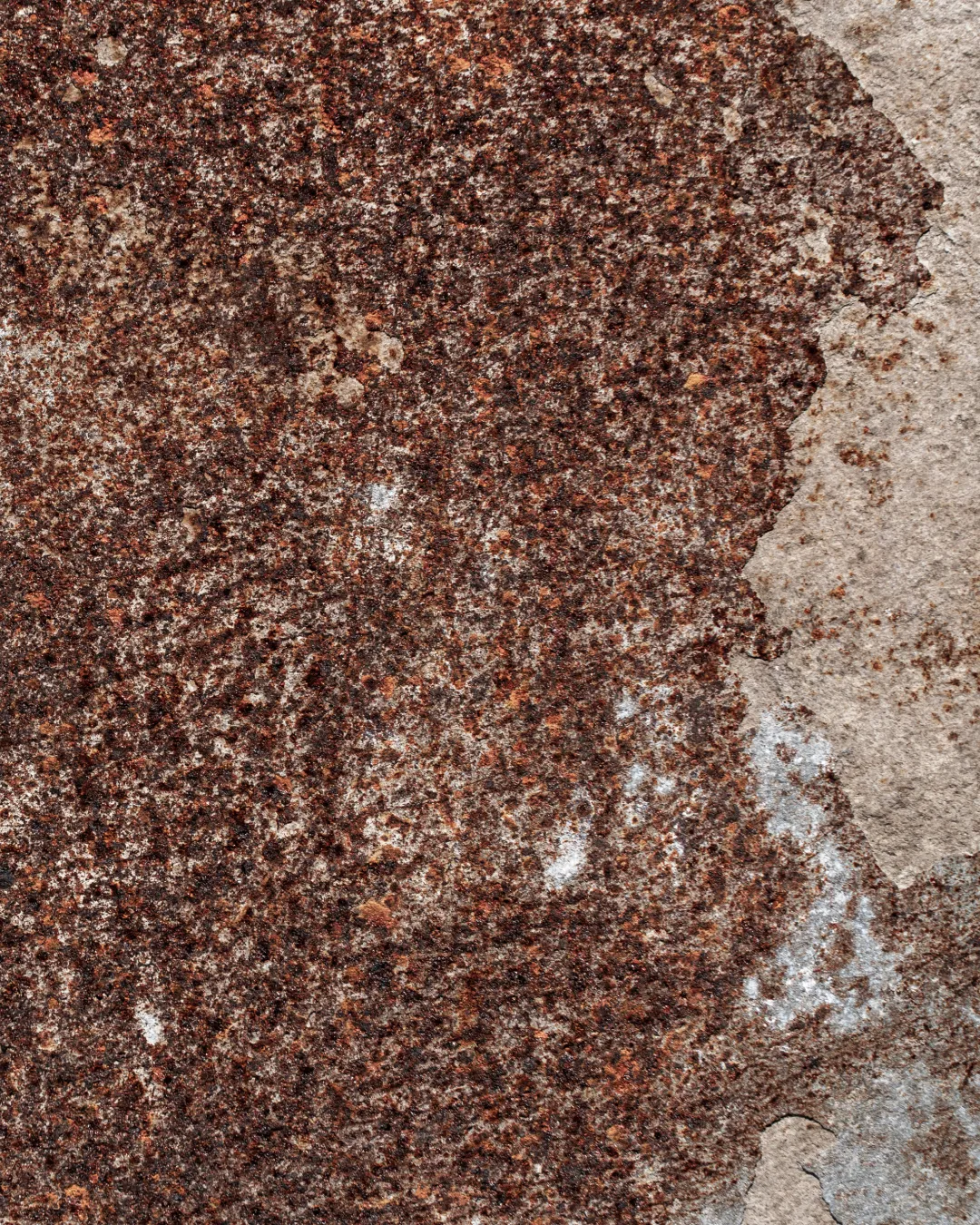
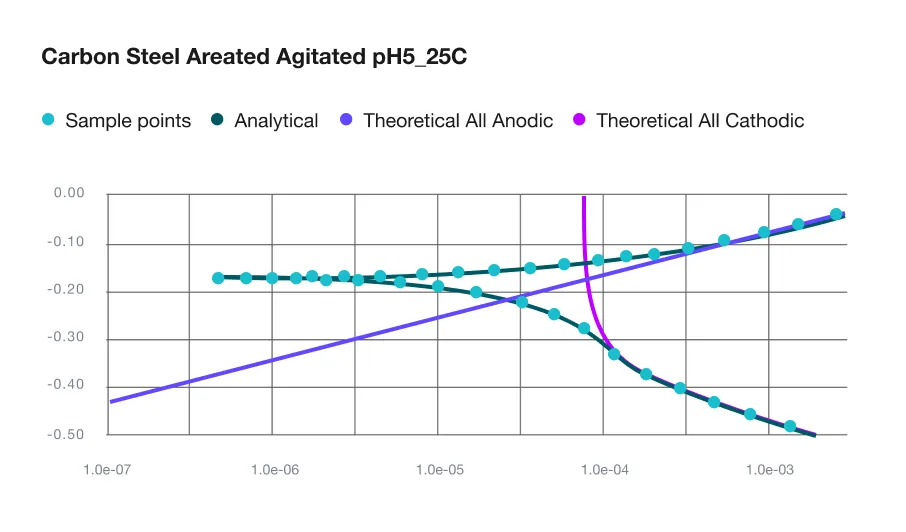
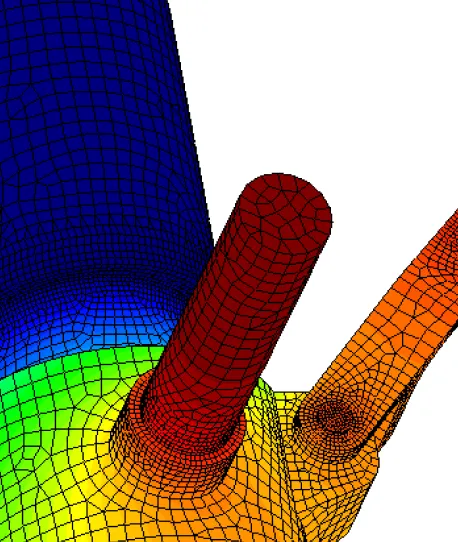
Safeguarding structures is a vital role of corrosion management and cathodic protection simulation.
Corrosion is an electrochemical process that is a perpetual threat to structural integrity. Overtime structures and components can weaken which could lead to catastrophic failure. In industries exposed to harsh environments, managing and predicting corrosion patterns within your asset is of utmost importance.
Our simulation software and engineering consultancy stand as beacons of excellence in simulating cathodic protection, corrosion management, and assisting the optimal design of sacrificial and impressed current cathodic protection (ICCP) systems. Working with industries that shape the world, we enable our clients to forge ahead with confidence, knowing that their engineering projects are supported by decades of experience, and a passion for innovation.
CP Digital Twin
BEASY CP Digital Twin provides corrosion and cathodic protection engineers with the data needed to make fast and informed decisions and provides actionable simulation insights into operations. With a digital twin, engineers can determine the ideal design before the asset goes into operation. Integrity engineers can react to anomalies based on the predicted health management information and deep insights gained from the digital twin.
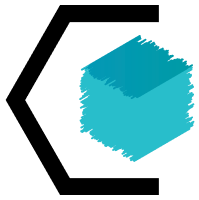
Corrosion Manager
BEASY Corrosion Manager is the most advanced software for foreseeing corrosion rates, corrosion currents, and polarisation potentials within three-dimensional galvanic corrosion models. Tailored for structures immersed in either bulk or thin electrolyte environments, this exceptional solution is particularly adept at addressing atmospheric corrosion scenarios. Confidently anticipate corrosion rates with BEASY Corrosion Manager.
AC Interference
An advanced tool for pre-emptively estimating induced voltages within pipelines situated beneath low-frequency overhead power lines, AC Interference can calculate potentials induced along pipelines as a result of alternating current (AC) flowing through high-voltage overhead powerlines in close proximity. Produce fast results and anticipate anomalous potential disruptions along a pipeline.
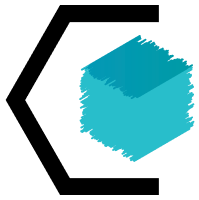
Corrosion & CP
BEASY Corrosion and Cathodic Protection (CP) is a cutting-edge solution meticulously crafted to replicate the intricacies of galvanic corrosion challenges and cathodic protection strategies. Unlock the power of BEASY CP to delve into corrosion analysis and monitor the effectiveness of a chosen cathodic protection system. Suitable for both offshore and onshore fully immersed electrolyte environments.
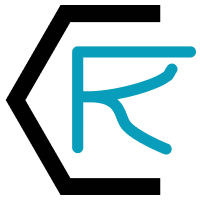
PolCurveX
PolCurveX is the ultimate polarisation data management solution. Unveil the intricacies of material behaviour using deconvolution for better support of recent MIL-STD-889-D standards. With PolCurveX, effortlessly import, export, store, and manipulate polarisation data across a diverse range of formats. Seamlessly interact with this essential tool that perfectly complements BEASY Corrosion Manager.
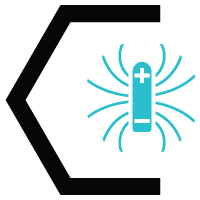
UEP & CRM Signatures
BEASY’s Signature Management solutions provide a comprehensive solution for engineers wishing to predict and manage corrosion related electric and magnetic fields. Corrosion related electric (UEP) and magnetic fields (CRM) have an important role in the design of naval vessels and their associated signatures.
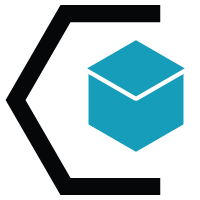
Other
Along with BEASY’s extensive range of stand-alone software, we offer a variety of add-ons to assist engineers and systems designers with their workflow and processing. This also allows models created in third-party software to benefit from BEASY’s powerful simulation and time-stepping capabilities.
Industry Leading Detection & Prevention For You
BEASY's software products and services help organisations solve complex engineering challenges.
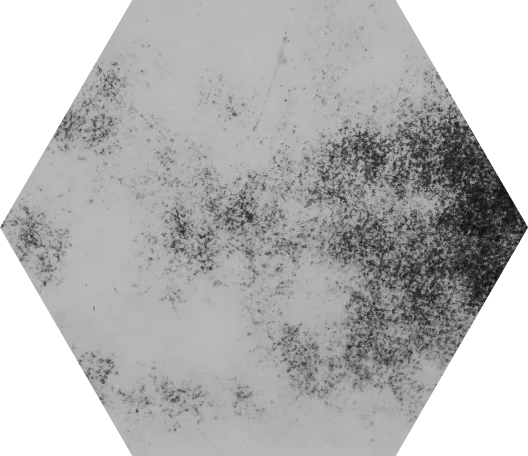
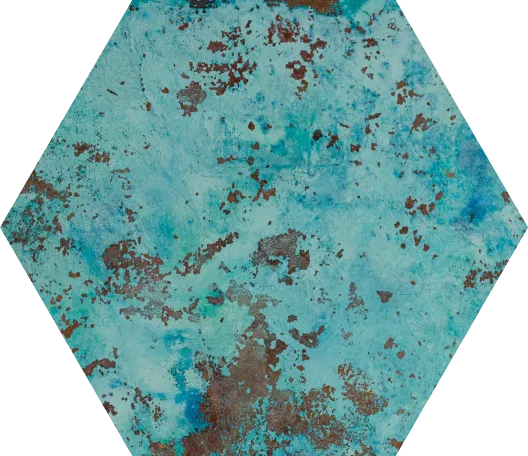