Corrosion Manager

BEASY Corrosion Manager enables engineers to quickly assess the risk to components and structures of galvanic corrosion and the effectiveness of surface protection systems. The software can predict the location and severity of the galvanic corrosion which can occur when dissimilar metals or certain types of composites are located in conjunction with each other.
Corrosion management software provides a range of benefits to engineers working across a variety of industries, including improved data management, risk assessment, predictive maintenance, cost savings, and compliance with regulations. Ultimately, BEASY Corrosion Manager assists companies in maintaining the integrity and longevity of their assets while optimising resource allocation.
The geometry of the materials, the characteristics and extent of the electrolyte including thin films such as atmospheric, deep, and crevice, and the type of mitigation methods employed affect the extent and rate of corrosion. BEASY Corrosion Manager enables engineers to replace the “Find it and Fix it” mindset with a “Predict & Prevent/Manage” approach based on understanding of the physics combined with the ability to predict the corrosion behaviour for a range of structures and conditions.
With BEASY Corrosion Manager incorporating the electrochemical behaviour and geometrical effects, it is inherently more realistic, and informative, than simply comparing potential difference in the electrochemical series.
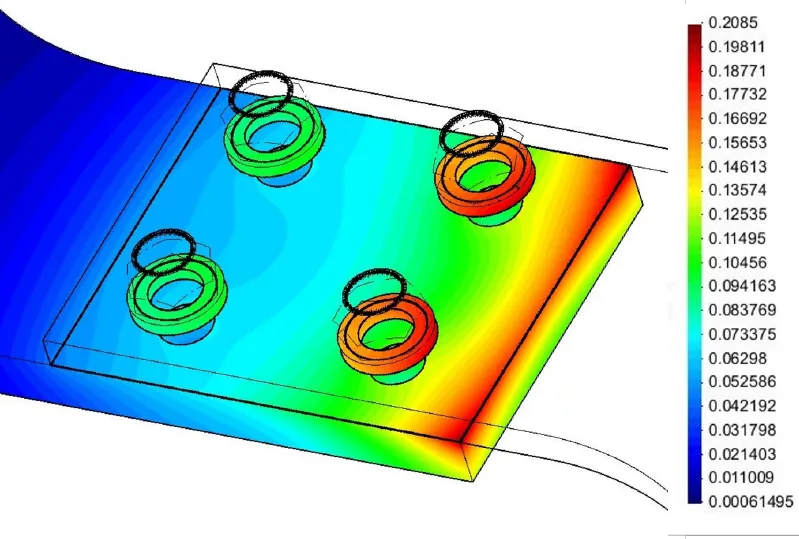
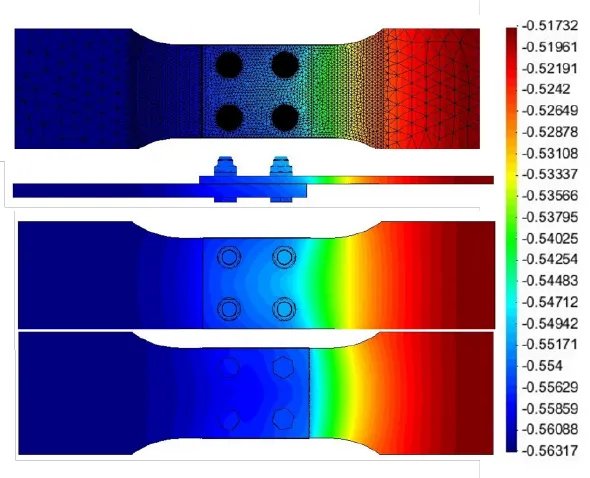
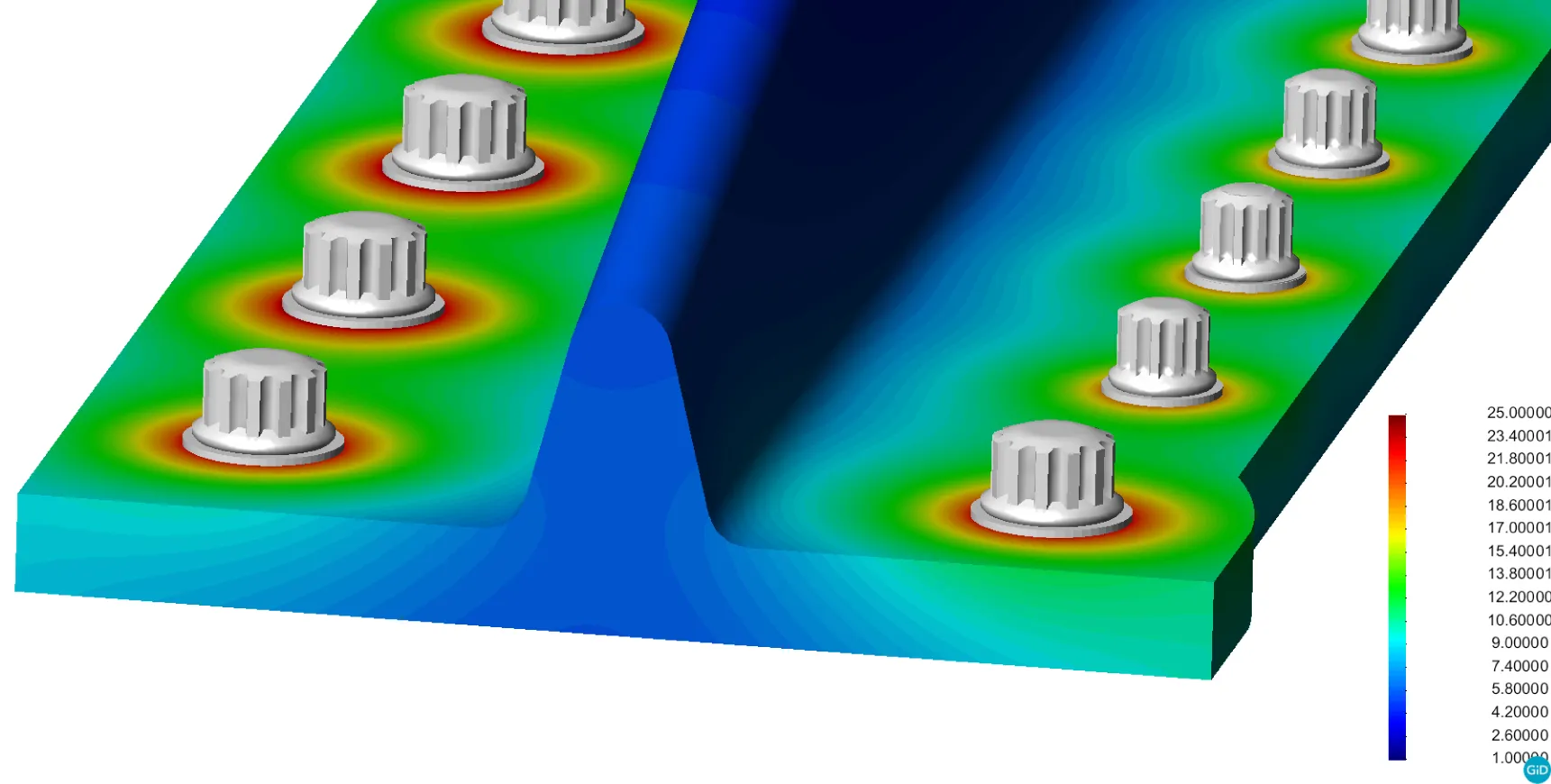
Elevate your expertise
BEASY offers a variety of training options: from comprehensive full courses, to webinars and tailored training program, our experts in corrosion and fracture ensure that you get the most out of BEASY's software.